Modern commercial design is witnessing a shift, driven by innovative building envelopes that deliver on aesthetics, functionality, and sustainability. The Forsyth Pointe project featured here is a testament to this evolution, showcasing how architecture is not only changing the city’s skyline but also reshaping its identity. Continue reading to learn about the challenges faced during its development, the successes achieved, and the broader implications for commercial design.
The vast plains of the Midwest have always borne witness to transformation—from the progression of the frontier days to the urban revivals of this century. Nowhere is this metamorphosis more apparent than the prominent business district of Clayton, Mo., an area fast becoming known for the architectural prowess of its changing skyline.
In the realm of commercial real estate, modern office developments such as Forsyth Pointe in Clayton are raising the bar. As reported in the St. Louis Business Journal, the project represents a notable “flight to quality” trend which has taken full effect among tenants. Beyond a mere affinity for new facilities, there is a marked demand for buildings that exude high-end amenities and architectural features. Increasingly, today’s tenants prioritize office space that echoes their brand’s ethos—spaces where quality, innovation, and sustainability are not just buzzwords but tangible facets.
Look no further for an example of this trend than Emerson Electric’s decision to relocate its company headquarters to Forsyth Pointe, which is already nearing capacity after opening earlier this year.
Featuring a 0.4-ha (1-acre) garden terrace with putting greens, a fire pit, to custom-designed benches, and a fitness center, the $250 million Forsyth Pointe complex embodies a contemporary design. While the interiors of such buildings speak volumes about what their occupants value, it is their exteriors—particularly the envelopes—that often make the most immediate and lasting impressions.
Beyond the surface
Building envelopes, historically seen as a blend of aesthetics and protection against external elements, have evolved. Today, it is not just about the allure, but also about the immediate functionality and sustainability they offer. These essential components put the building exterior front and center, creating a powerful first impression amidst a fluctuating real estate market.
Yet, quality in modern building design transcends outward appearance. Beyond aesthetic allure, the caliber of a building is gauged by its functionality—particularly by its ability to regulate internal climates and improve energy efficiencies. Such is the indispensable role of the building envelope in contemporary architecture. Forsyth Pointe exemplifies this with its performance-based design approach, employing high-performance glazing and state-of-the-art insulation methods that not only bolster energy efficiency, but also adhere to stringent performance criteria. This technical foresight allows the integration of architectural elements that harness natural light and mitigate heat gain, a testament to the project’s commitment to sustainable practices.
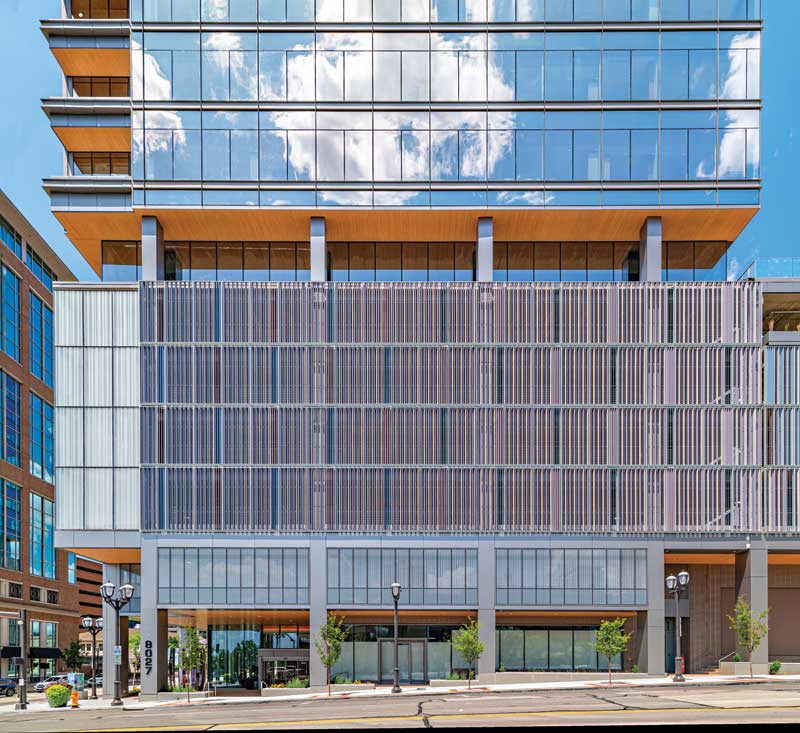
Pushing boundaries with facade installation
Specializing in providing building enclosure services, IWR North America’s involvement with Forsyth Pointe showcases how specialty contractors play a pivotal role in bringing these new-age architectural visions to life. The expertise is not just in doing the work, but in navigating the unique challenges each project presents and devising innovative solutions.
Crafted by Christner Architects, the vision for Forsyth Pointe was unequivocal: large units of glass, seamlessly integrated into the building, providing both form and function. This glass curtain wall exemplifies the high-end nature of the development and contemporary architectural trend that embraces large, transparent sections to maximize light and view.
To bring this architectural vision to life, IWR North America was tasked with the installation of 27,406 m2 (295,000 sf) of curtain walls. The complexity of Forsyth Pointe’s facade was not merely in its size but in coordinating 23 distinct systems that contribute to the building’s thermal, structural, and aesthetic integrity. From the transparency of high-performance glazing to the engineering of metal panels and attachment assemblies, each component played a critical role in the overall design.
Crafting elegance with cladding and integration
Forsyth Pointe features the integration of opaque assemblies and glazed systems, presenting a facade that intertwines a palette of diverse materials—from wood-look soffits to aluminum composite material (ACM) panels and oversized glazed units. Each element is thoughtfully coordinated, with transitions between materials crafted to achieve a visually unified structure that embodies the architectural vision down to the finest detail.
Rick Neal, IWR’s project superintendent with 25 years of glazing expertise, oversaw the merger of elements that formed the upper floors of the office towers. The challenge laid in the confluence of materials—where the unitized curtain wall of the high rises met the unique glazing of lower levels, and where balconies interplayed with glass railings; all demanding a seamless orchestration of transitions. This dedication to cohesive design extended to the inclusion of features such as custom aluminum column covers, which offered both elegance and functional strength.
The crux of Neal’s task was ensuring all components conformed to the precise design intent. The alignment of multiple materials, each with its own lines and characteristics, had to present sightlines consistent with the facade’s vision. This alignment was not confined to adjacent materials but was part of a continuous line—such as the ACM band that crowned the top floors, dipped into terraces, and re-emerged in the glazing assemblies below. To realize this design, it was imperative for teams to work in tandem, with the glazing and sheet metal superintendents operating in lockstep to maintain the architect’s envisioned sightlines.
Adding to the complexity, the towers’ rooflines featured an elaborate metal band that wrapped the top, marking the convergence of glass sections—an aspect that posed considerable access challenges. Neal recounted the precise planning required to navigate the urban landscape beneath, ensuring the team’s movements were not only efficient but also safe. This undertaking highlighted the critical nature of coordinating multiple disciplines and specialties to uphold the seamless aesthetic continuity while adhering to stringent safety standards.
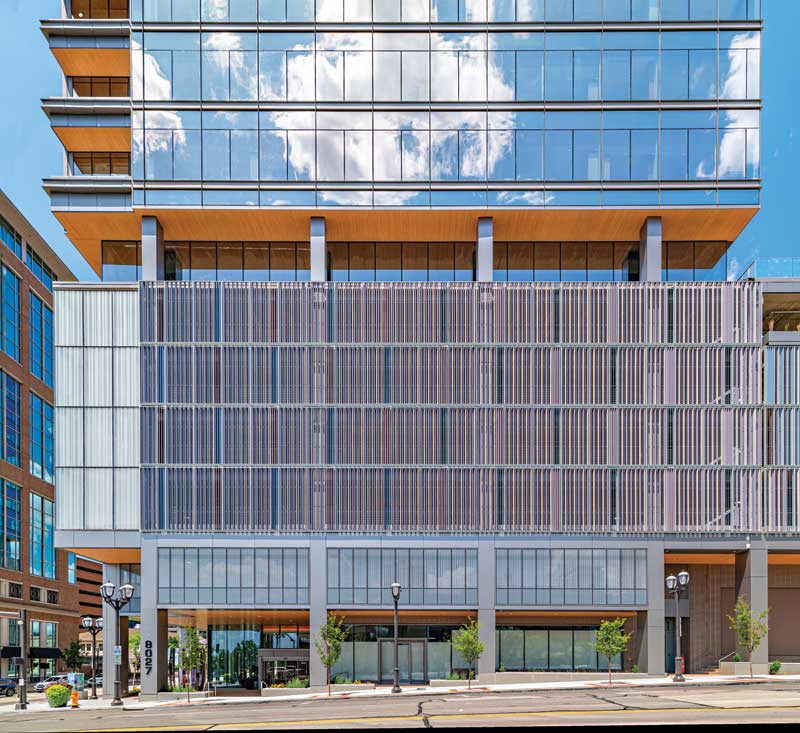
Problem-solving amidst urban constraints
Building for tomorrow, today
Forsyth Pointe rises in the heart of Clayton, transcending the role of mere architectural achievement to embody the modern marvels propelling innovation in commercial design. Embracing collaboration at every turn, it demonstrates that architecture today is not just about constructing buildings—it is about sculpting spaces that reflect aspirations, values, and the pulse of evolving communities.
The building envelope of Forsyth Pointe emerges as a striking declaration in its own right. As it gracefully rises against Clayton’s urban backdrop, it underscores the synergy between function and artistry in today’s architecture. In an age of transforming cityscapes, similar structures serve as inspiration and as reminders that the built environment is more than the sum of its materials. These structures stand as testaments to visionary thinking and the collective resolve that breathes vitality into them, charting a path toward a future where commercial design seamlessly integrates with ambition and innovation.
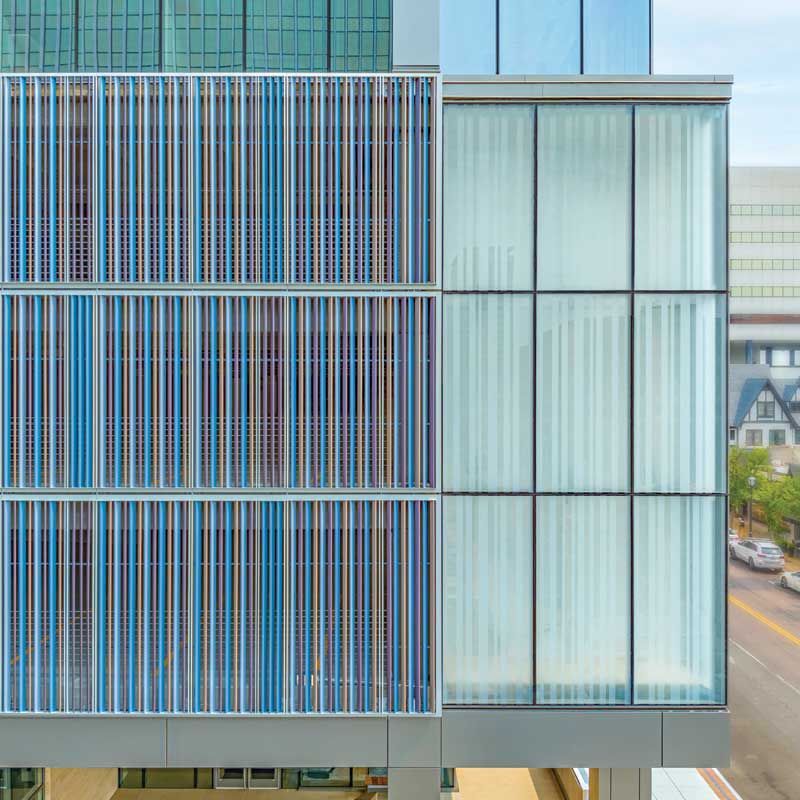